Microrobotic Visual Control of Motile Cells using High-Speed Tracking System
Summary
Microorganisms have smart built-in sensors and actuators in their bodies. Our goal is to control microorganisms as micro-scale smart robots for various applications. As a first step, we have developed a visual feedback control system for Paramecium caudatum cells.
In order to ensure both detailed measurement and a large working space, lock-on tracking of a free-swimming cell with high frame rate is essential. In our system, high-speed (1-kHz frame rate) tracking hardware and software are used for continuous observation of moving cells with high magnification. Cells swim in a chamber, and their positions and other properties are measured and computed in real time. The chamber position is visually controlled automatically to track a specific cell. The cell motion is controlled electrically by utilizing the galvanotaxis (intrinsic reaction to electrical stimulus) of microorganisms. Experimental results for open-loop control (periodic zigzag motion) and closed-loop control (trapping within a small region 1 mm wide) demonstrate the possibility of using microorganisms as micromachines.
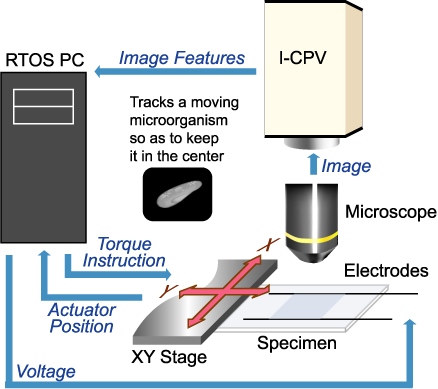
Experimental Results
We used Paramecium caudatum cells, which tends to swim toward the cathode (the negative pole).
Open-Loop Control
First, open-loop control of cells was performed. Cells were controlled by a time-varying stimulus whose pattern was fixed in advance. The electrical stimulus was applied, and reversed every 6 s. The strength of the voltage gradient was 4.1 V/cm (9 V across a 22mm gap).
The left plot shows the X position (parallel to the electric field) of cells in the open-loop control experiment. Arrows indicate the direction of the applied electric field. The right plot shows the trajectory of cell #3, and its orientation (small arrows), where the direction of the electric field is horizontal. The spiral path and the ever-changing orientation of the cell were reconstructed with high fidelity. It also indicates that both high magnification and good trackability over a large working area were achieved.
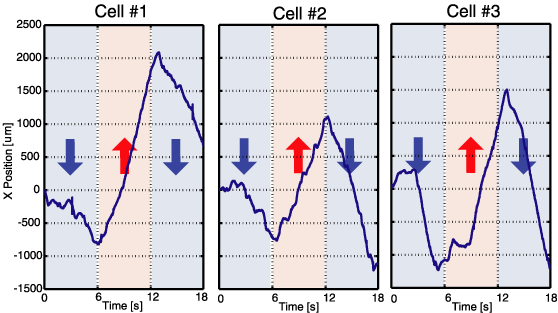
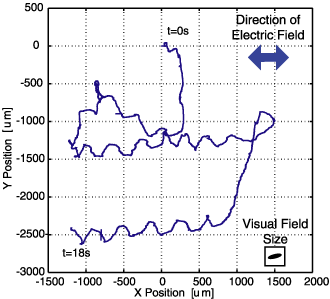
Closed-Loop Control (Trapping)
In order to confirm the ability of closed-loop visual feedback control of cells, we performed a simple trapping experiment; the stimulus was adjusted in real time according to the target status. The width of the trapping region was set to 1 mm. The voltage was reversed when the cell moved out of the boundaries. Other conditions were the same as those of the open-loop control experiment described above.
The plots below demonstrate results of the control experiment, where the blue area is the trap region. The left plot shows the time sequence of both the voltage and the position parallel to the field (X), and the position perpendicular to the field (Y). The voltage was reversed when the cell went out the region. Consequently the cell swam back and forth in the region. The trajectory of the cell is shown in the right plots.
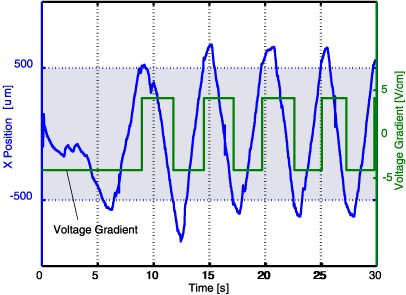
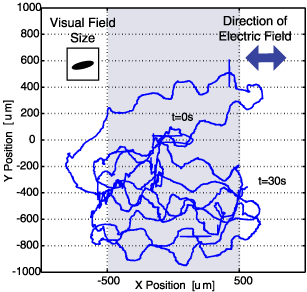
These results indicate that we achieved continuous open-loop and closed-loop control of galvanotaxis of motile cells by target tracking. It is a first step for realizing microrobotic system composed of microorganisms.
References
- Naoko Ogawa, Hiromasa Oku, Koichi Hashimoto and Masatoshi Ishikawa. Microrobotic Visual Control of Motile Cells using High-Speed Tracking System. IEEE Transactions of Robotics, Vol. 21, No. 4, Aug. 2005. [PDF (1.1M)] *IEEE (caution: the PDF version on IEEE Xplore has a typo in the issue number and month in its header.)
- Naoko Ogawa, Hiromasa Oku, Koichi Hashimoto and Masatoshi Ishikawa. Motile Cell Galvanotaxis Control using High-Speed Tracking System. 2004 IEEE International Conference on Robotics and Automation (ICRA 2004) (New Orleans, USA, 2004.4.28) / Proceedings, pp. 1646-1651, Apr, 2004. [PDF (1.7M)] *IEEE
Corresponding author: Naoko Ogawa
(Naoko_Ogawa)