Robotic Needle Threading Manipulation based on High-Speed Motion Strategy
Summary
Realizing accurate robotic manipulation of flexible objects is very challenging. It asks for dexterous manipulation skill, and demands good adaptation to dynamic uncertainties due to deformation. Unlike traditional methods that basically depend on complex modeling, we follow the opposite approach by exploring possible simplifications based on high-speed motion strategy as well as high-speed visual sensing. As an application task concerned with robotic needle threading, this work demonstrates our philosophy by proposing a novel and straightforward high-speed strategy to speed up the manipulation while solves the issue of deformation uncertainty at the same time. The methodology is based on a very simple physical fact, namely that by rotating a thread with sufficient velocity, the thread can be approximated as a rigid object caused by the constantly applied centrifugal force during the rotation. Therefore, the needle threading problem is converted into a simpler peg-insertion problem, and the complexity of interaction between robot and deformable thread is significantly simplified. Based on the proposed strategy, simple technical methods then become possible for adoption to accomplish the challenging task. Experiments show that the proposed approach allows the needle threading task to be realized very rapidly.
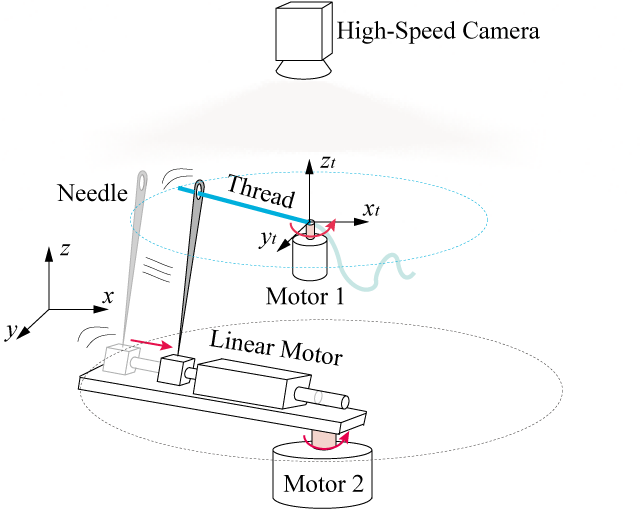
Proposed Concept
Movie
If you want to use the original video, please send an e-mail for copyright permission to contact .
Reference
- Shouren Huang, Yuji Yamakawa, Taku Senoo and Masatoshi Ishikawa: Robotic Needle Threading Manipulation based on High-Speed Motion Strategy using High-Speed Visual Feedback, 2015 IEEE/RSJ International Conference on Intelligent Robots and Systems (IROS2015) (Hamburg, 2015.9.30)/Proceedings, pp.4041-4046